Introduction
Yet again, a barreling crack has appeared during production!
“There’s no way we can keep the line running like this!” The production floor echoes with frustration.
But here come our heroes: The Amazing Keni and AI Steel Cat!
This time, they’re up against a crack that’s different from anything they’ve encountered before.
Dialogue: A Deep Dive into the Crack’s Root Cause
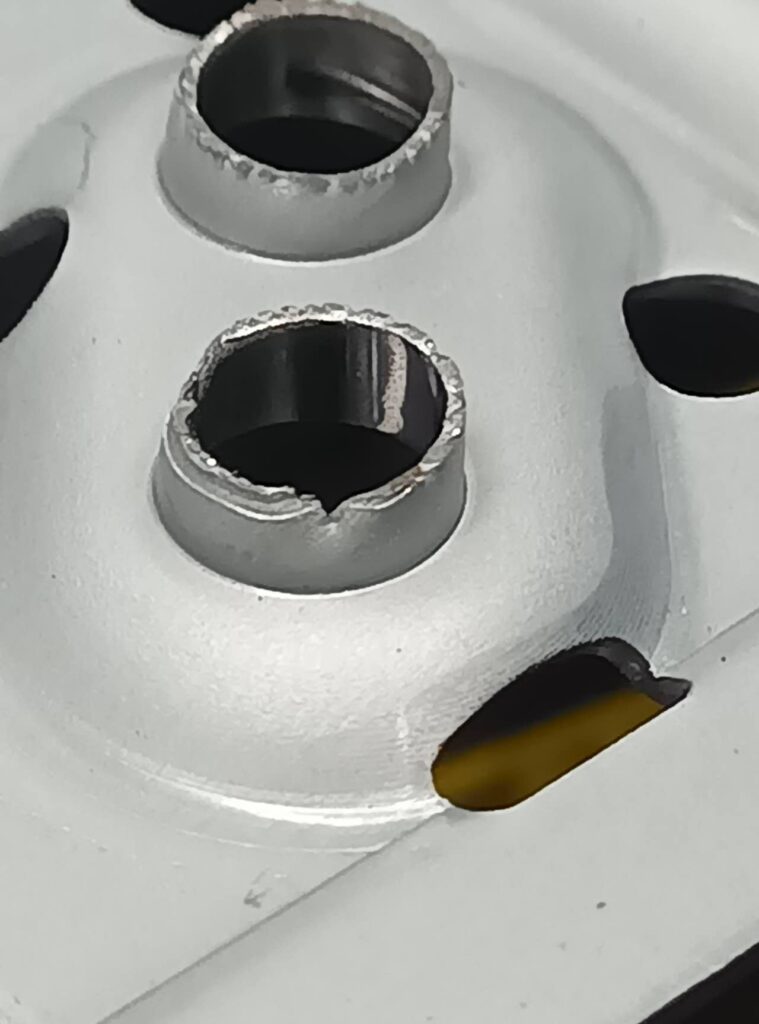
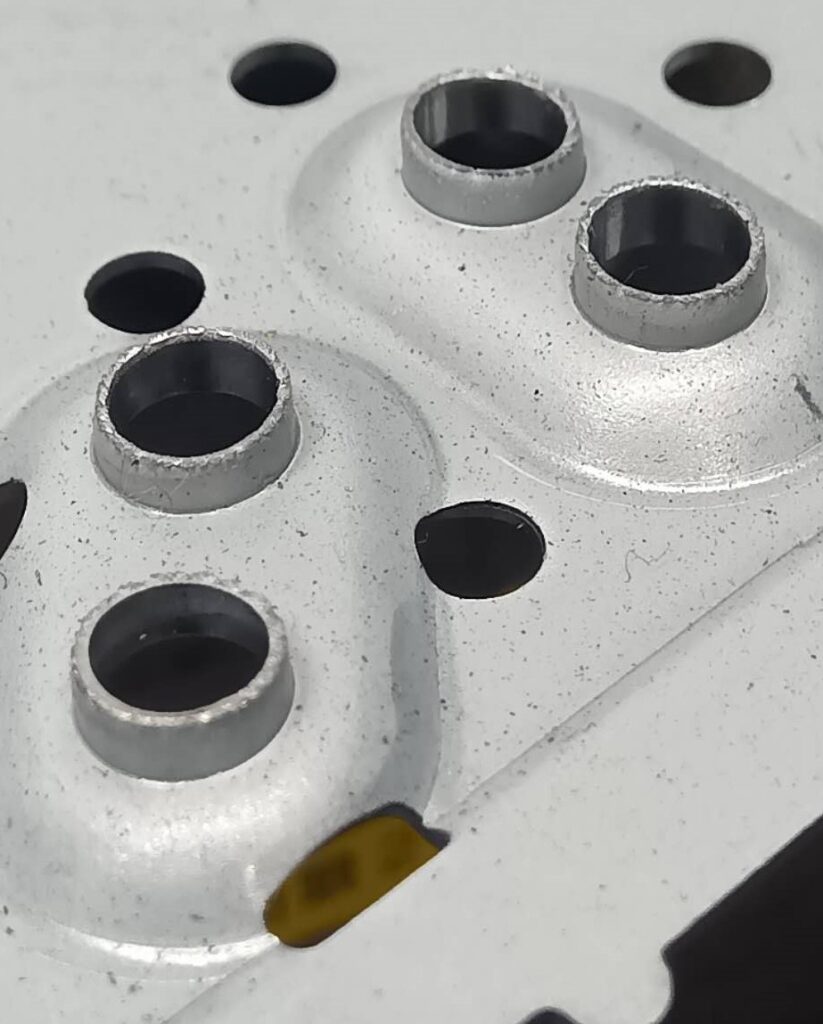
The Amazing Keni:
“Hey, AI Steel Cat! We’ve got another crack! And this time, it’s acting weird.
How the heck are we supposed to deal with this barreling crack? Readers, what would you do? Help us out here!”
AI Steel Cat:
“Whoa, this is a serious situation! Alright, let’s go over the known causes first!”
- Material stretch limit: If the flange stretches too much during processing, it cracks.
- Burr on the hole: Burrs on the outside increase the chance of cracking.
- Localized stretching: Harder materials can crack due to localized overstretching.
- Improper processing conditions: Inappropriate processing speed or lubricant can cause cracks.
The Amazing Keni:
“Yeah, that’s all good, but there’s more to it than just that.”
Change Your Perspective: Comparing with the Last Incident
AI Steel Cat:
“Come to think of it, we had a similar crack issue last time, didn’t we?
Back then, the root cause was a loose lower punch, so we reinforced the stripper block and springs.”
The Amazing Keni:
“Yep, good memory. It was a similar situation, for sure.”
AI Steel Cat:
“So, could it be the same issue this time?”
The Amazing Keni:
“Nope. This time, the crack’s location and pattern are completely different.”
AI Steel Cat:
“Different location and pattern…? What do you mean?”
The Amazing Keni:
“Last time, the crack spread evenly because of the punch’s looseness.
But now, the crack starts from two separate points, and it’s advancing before the ironing stage even begins.”
AI Steel Cat:
“Aha! So, the issue isn’t with the ironing process itself.”
The Amazing Keni:
“Exactly. We need to consider another cause.”
Uncovering the Hidden Factors at the Production Site
AI Steel Cat:
“Alright, Amazing Keni, let’s list the unique site factors that could be affecting this process. For example—”
- Hole position deviation: Even a 0.1mm misalignment can increase crack risk.
- Punch scratches: Scratches on one side cause the punch to shift off-center.
- Punch entry direction: If the punch enters from the side with burrs, cracks are likely.
- Punch shape: Shapes like bullet, tapered, semi-round, or flat have different effects.
- Surface roughness: Rough surfaces on the punch tip can be fatal.
The Amazing Keni:
“Exactly! Plus, insufficient localized lubrication or incorrect processing speed can make things worse.”
Reviewing Previous Countermeasures
AI Steel Cat:
“Let’s review the countermeasures we’ve already tried!”
The Amazing Keni:
“Alright, here’s what we’ve done so far—”
- Polished the punch tip
- Fixed the burrs and fracture surfaces on the hole
- Added localized lubrication
- Checked the material hold timing (no abnormalities found)
- Inspected the stripper block (no issues)
- Verified punch and die alignment (all good)
- Adjusted the punch position by 0.5mm—no improvement
AI Steel Cat:
“Wow… and still no results? This crack is a tough nut to crack!”
The Amazing Keni:
“You bet. But after a lot of observation, I finally figured out the root cause.”
The Core Issue: Timing Mismatch
The Amazing Keni:
“The crack was forming during the hole expansion phase.
Localized stretching exceeded the material’s limit because the excess material wasn’t flowing fast enough.”
AI Steel Cat:
“Oh, so we need to speed up the material flow, right?”
The Amazing Keni:
“Exactly! That’s why I modified the punch tip to a flat-topped shape.”
AI Steel Cat:
“Nice! Did it work?”
The Amazing Keni:
“Yep, the crack has significantly reduced. We also added a guide protrusion on the punch to prevent positional misalignment.”
AI Steel Cat:
“Wow, Amazing Keni! Your site knowledge is pure gold!”
Conclusion Narration
This time, the root cause was a timing mismatch and stripper block tilt.
Thanks to the teamwork between The Amazing Keni and AI Steel Cat, the issue was resolved!
Production is back on track.
The Amazing Keni:
“Now we can finally keep production running smoothly!”
AI Steel Cat:
“Crack problem? More like cracked problem solved! But the adventure’s not over yet!”
The Amazing Keni:
“That’s right… Cracks are our eternal challenge!”
Closing Words
Once again, The Amazing Keni and AI Steel Cat have brought peace to the production floor.
Readers, let’s keep smiling and solving challenges together—one crack at a time! 🐾✨
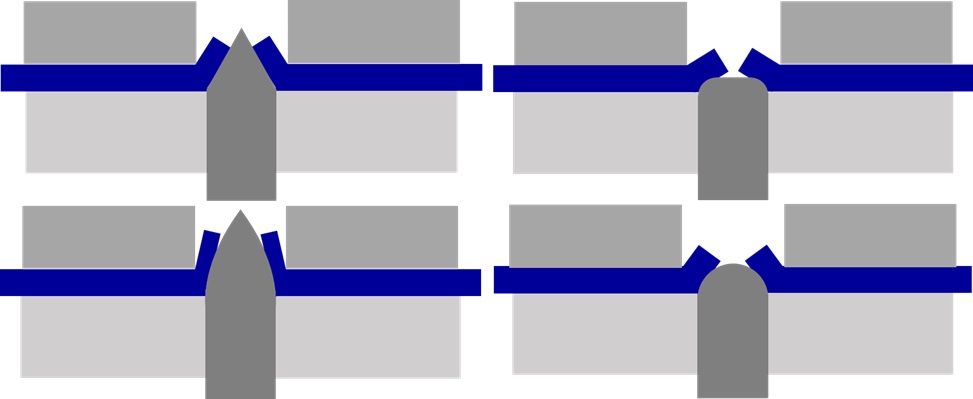
1. General Information: Causes of Barreling Cracks
Commonly cited causes of barreling cracks include:
- Exceeding material stretch limits:
The flange may crack if it stretches too much during the process. - Burrs on the hole:
Cracks can develop if the burr is on the outside of the hole. - Localized stretching:
Harder materials may experience cracking due to excessive localized stretching at the tip. - Improper processing conditions:
Incorrect processing speed or lubricant selection can lead to cracks.
2. Specific Factors Identified by The Amazing Keni
Processing Factors:
- Hole position misalignment: Even a 0.1mm shift can increase crack risk.
- Punch scratches: Scratches on one side of the punch may cause the center to shift, leading to cracks.
- Entry direction: When the punch enters from the die side, burrs may form on the outside, increasing crack risk.
- Fracture surface of the hole: This can act as a trigger for cracking.
Punch-Related Factors:
- Punch tip shape: Bullet, tapered, semi-round, and flat types produce different crack patterns.
- Surface roughness: A rough punch tip surface can severely impact processing quality.
Other Factors:
- Processing speed: Inconsistent speed increases the likelihood of cracks.
- Lubrication: Only using roller lubrication may result in insufficient localized lubrication, influenced by both the type and amount of oil used.
3. Details of the Current Case
Processing Conditions:
- Material: SPCE, thickness 0.8mm
- Hole dimensions: Φ2.4 (for M5 thread tapping, hole Φ4.57)
- Punch type: Bullet-shaped
- Structure:
- Lower: Barreling punch with a localized stripper block.
- Upper: Barreling die, knockout system (peeling mechanism), and stripper block.
Other Processes:
- The stage includes additional processes such as small and angle bending, and 18 other barreling points, which may impact the process.
Lubrication: Roller lubrication only (no localized lubrication).
Equipment: 400T progressive press, SPM 25.
4. Implemented Countermeasures and Results
Despite implementing the following countermeasures, the issue persisted:
- Polishing the punch tip.
- Fixing the burrs and fracture surfaces on the hole.
- Adding localized lubrication.
- Investigating the timing and movement of material hold (no abnormalities).
- Verifying the state of the upper stripper die (no issues).
- Checking the punch and die alignment (no issues).
- Shifting the punch position by 0.5mm—no improvement.
5. Observations from the Defect Phenomenon
Further observations revealed the following:
- Cracks were more pronounced on the side with less ironing.
- Cracks developed from two points and progressed independently of the highly ironed area.
- The cracks were already advancing before the ironing stage.
6. Identified Cause
The investigation concluded that the issue was related to the timing of hole expansion.
To address this, the solution focused on accelerating the flow of excess material at the punch tip during hole expansion.
- Effective Countermeasure:
Modifying the punch tip shape to optimize the timing of hole expansion and ironing.
Additionally, it was found that the tilting of the stripper caused one-sided contact, exacerbating crack formation.
Since structural modifications were not feasible, the focus shifted to optimizing the punch tip shape.
7. Adopted Countermeasure
The punch shape was changed to a flat-topped design, which accelerates the ironing process.
Points to Note:
- This design may cause misalignment between the punch and die.
- To mitigate this, a guide protrusion was added to the center of the punch to maintain alignment.
8. Conclusion
The root cause of the defect was a mismatch in the hole expansion and ironing timing.
By modifying the punch shape, the team significantly reduced crack formation, even under conditions where the stripper tilt could not be completely corrected.
Bonus Section: The Impact and Effectiveness of Punch Shapes
According to Misumi technical information, barreling punches typically have bullet-shaped tips. However, other shapes also influence processing results.
Key Points:
- Punch shape affects barreling height and processing force, playing a crucial role in crack prevention.
- The timing of hole expansion and ironing is critical.
- Shapes that accelerate ironing improve material flow and reduce the risk of cracks.
By carefully adjusting the punch shape, manufacturers can achieve greater process stability and minimize defect risks. This level of precision can greatly impact the success of barreling operations!