Keni the Amazing: “Today, I’d like to discuss why burrs form in press punching. AI Steel Cat, can you explain the mechanism of burr formation as you understand it?”
AI Steel Cat: “Understood. I will provide a simple explanation.
In press punching, plastic deformation begins when the punch contacts the material. As the punch pushes through, compressive forces act on the upper side, while tensile forces act on the lower side, accumulating stress within the material. As a result, cracks form at the edges of the punch and die, progressing until the material is severed.
The cut surface consists of the following elements:
- Shear zone: The plastically deformed area.
- Fracture zone: The area where cracks propagate to separate the material.
- Burr: The portion of material stretched and left behind at the punch or die edges.
The following factors contribute to larger burr formation:
- Improper clearance settings.
- Wear on the cutting edges.
- Material properties and processing conditions.
These factors interact, leading to burr formation.”
Keni the Amazing: “I see. You’ve explained the conditions under which burrs form, but you haven’t quite addressed the fundamental question: why do burrs form in the first place?”
AI Steel Cat: “You’re right. I described the factors that increase burr size but didn’t fully explain the root cause of burr formation. Let me clarify:
When the material is severed, if the cracks do not propagate properly, excess material is stretched, resulting in burrs. The primary causes of this are:
- Blunting or wear of the cutting edge.
- Improper clearance settings.
- Material flow into the cutting edge.
In short, burrs form because cracks fail to propagate cleanly along the cutting edges, leaving behind excess material.”
Keni the Amazing: “I see. But I have a few concerns:
- What exactly does ‘proper crack propagation’ mean?
- What is happening when ‘excess material is stretched’?
- How do we explain that burrs form not only on the retained side but also on the slug side?”
AI Steel Cat: “Good questions. Could you elaborate on these points?”
Keni the Amazing: “Sure, let me explain.
First, when the punch contacts the material, plastic deformation begins, and compressive stress builds up. As the punch progresses, the material beneath the punch or at the die’s surface thins, causing compressive stress to decrease gradually. This stress then shifts to tensile stress, concentrating around the material’s corners and initiating a crack. The crack generally propagates at an angle of about 7 degrees toward the die side.
However, near the die, the material retains some compressive stress, which deflects the crack slightly away from the die. As a result, the crack extends into the clearance between the punch and die, causing the portion closer to the punch to become a burr. This explains the burr formation on the retained side.”
AI Steel Cat: “And what about the burr on the slug side?”
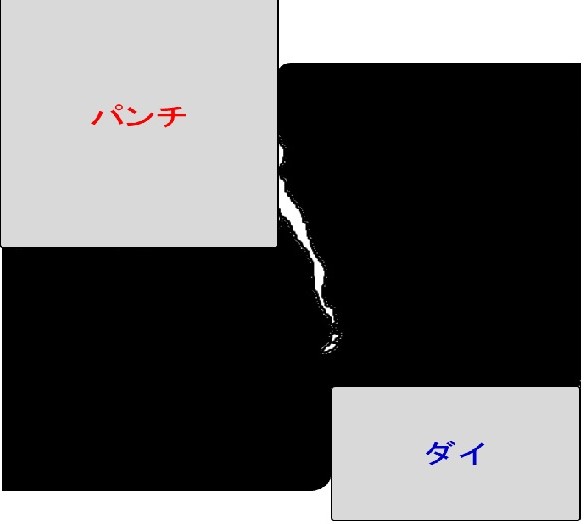
Keni the Amazing: “The burr on the slug side occurs because the crack initiates not from the punch’s corner but from a point slightly outside it. Since compressive stress is concentrated at the punch’s corner, the crack starts slightly outside this point. The offset amount determines the burr size.”
AI Steel Cat: “That makes sense. As you said, fully understanding burr formation requires analyzing real-world processing conditions and material properties in detail. I am always learning and evolving, and I recognize that there are still areas I cannot fully explain. I’d like to continue exploring this with you.”
Keni the Amazing: “That’s a good attitude. To suppress burr formation, it’s essential to manage the cutting edges, set proper clearances, and adjust clearances based on the punch shape. Let’s discuss specific countermeasures next time.”
AI Steel Cat: “Yes, let’s do that! I learned a lot today. Thank you!”
Keni the Amazing: “Likewise. See you next time.”