Introducción
Una vez más, apareció una grieta durante el proceso de barreling.
“¡No podemos continuar la producción con esto!” – se escucha en el piso de producción lleno de tensión.
Es aquí donde entran en acción El Asombroso Keni y AI Steel Cat. Esta vez, se enfrentan a una grieta diferente a las anteriores.
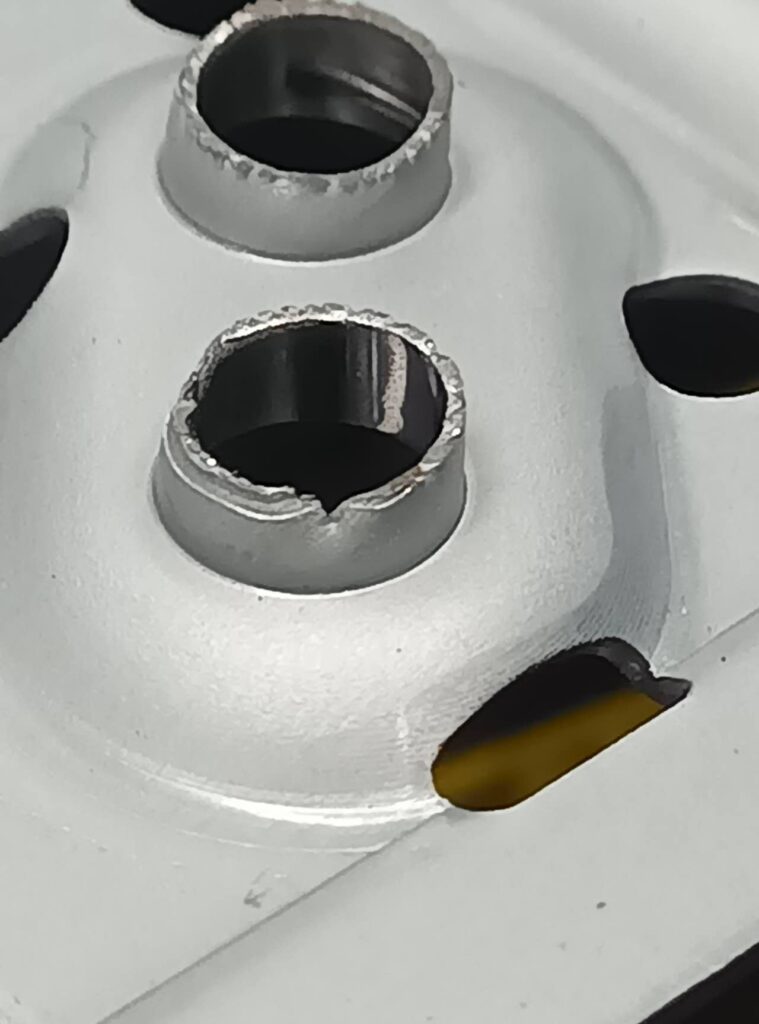
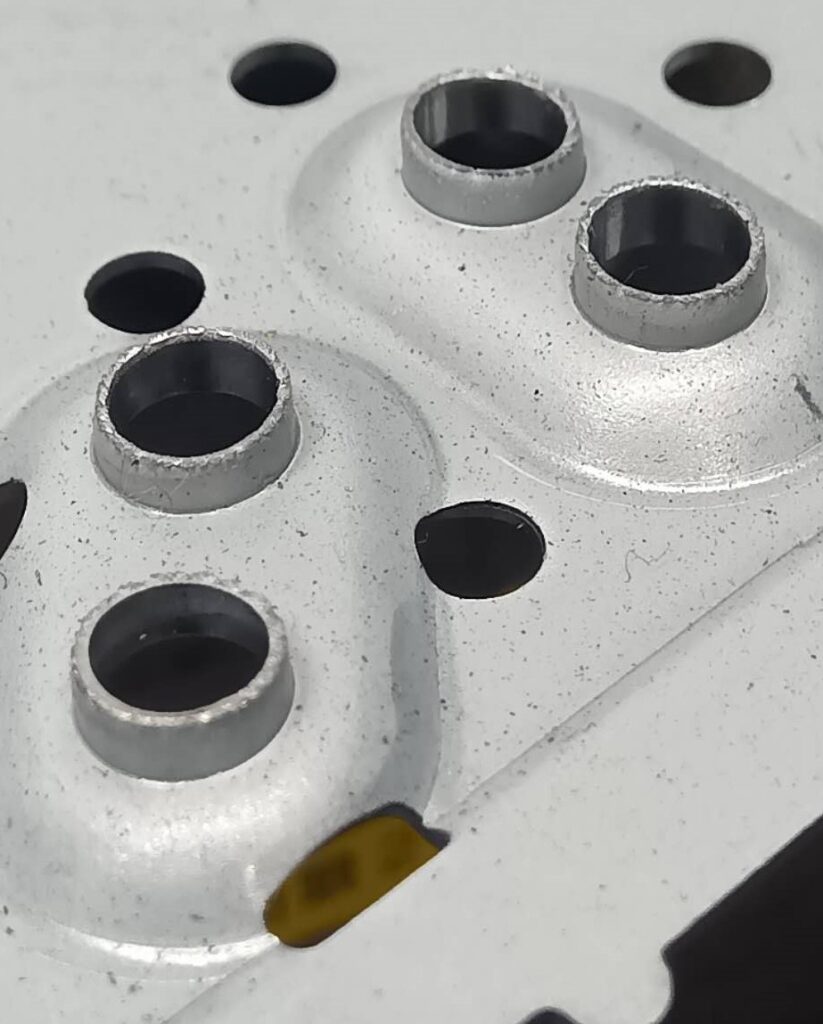
Diálogo: Investigando a fondo las causas de las grietas
El Asombroso Keni:
“¡Oye, AI Steel Cat! ¡Apareció otra grieta! Y esta vez, algo no está bien…
¿Qué está pasando con esta maldita grieta de barreling? ¿Qué harían ustedes, lectores? ¡Ayúdennos!”
AI Steel Cat:
“¡Esto es una emergencia! Repasemos las causas conocidas primero.”
- Límite de estiramiento del material: Si la brida se estira demasiado, se producen grietas.
- Rebarba en el agujero: Las grietas pueden aparecer si la rebarba está en el exterior.
- Estiramiento localizado: Los materiales más duros pueden agrietarse por estiramientos excesivos en ciertos puntos.
- Condiciones de procesamiento inadecuadas: Una velocidad o lubricación incorrecta pueden causar grietas.
El Asombroso Keni:
“Sí, eso es cierto, pero aquí hay algo más que no encaja del todo.”
Cambio de perspectiva: Comparación con la grieta anterior
AI Steel Cat:
“Recuerdo que la vez pasada también tuvimos un problema de grietas en el barreling, ¿no es así?
En esa ocasión, el problema fue un juego en el punzón inferior, y reforzamos el bloque stripper y los resortes.”
El Asombroso Keni:
“Exacto, te acuerdas bien. Fue algo parecido, sí.”
AI Steel Cat:
“¿Podría ser el mismo problema esta vez?”
El Asombroso Keni:
“No, esta vez es diferente. La ubicación y el patrón de la grieta son completamente distintos.”
AI Steel Cat:
“¿Ubicación y patrón distintos? ¿Cómo es eso?”
El Asombroso Keni:
“La vez anterior, la grieta se extendió uniformemente debido al juego en el punzón.
Pero ahora, la grieta comienza en dos puntos diferentes y se extiende antes de que comience el proceso de ‘ironing’.”
AI Steel Cat:
“¡Entiendo! Entonces el problema no está en el proceso de ‘ironing’ en sí.”
El Asombroso Keni:
“Correcto. Necesitamos identificar otra causa.”
Explorando los factores únicos del proceso
AI Steel Cat:
“Bien, Keni, organicemos los posibles factores únicos del sitio. Por ejemplo—”
- Desalineación del agujero: Una desviación de tan solo 0,1 mm puede aumentar el riesgo de grietas.
- Rasguños en el punzón: Los rasguños pueden desviar el centro del punzón.
- Dirección de entrada del punzón: Si el punzón entra desde el lado con rebarba, las grietas son más probables.
- Forma del punzón: Las formas como bala, cónica, semi-redonda o plana producen diferentes patrones de grietas.
- Rugosidad de la superficie: Una superficie rugosa en la punta del punzón es crítica.
El Asombroso Keni:
“¡Exactamente! Además, la falta de lubricación localizada o una velocidad de procesamiento incorrecta también pueden afectar.”
Revisión de las contramedidas anteriores
AI Steel Cat:
“Repasemos las contramedidas que ya implementamos.”
El Asombroso Keni:
“Claro, esto es lo que hemos hecho hasta ahora—”
- Pulimos la punta del punzón.
- Corrigimos las rebarbas en el agujero.
- Añadimos lubricación localizada.
- Investigamos el tiempo y el movimiento del material (sin anomalías).
- Verificamos el bloque stripper (sin problemas).
- Confirmamos la alineación del punzón y el dado (todo bien).
- Ajustamos la posición del punzón en 0,5 mm—sin resultados.
AI Steel Cat:
“¿Todo esto y aún nada? ¡Esta grieta es un hueso duro de roer!”
El Asombroso Keni:
“Lo sé, pero después de mucha observación, finalmente descubrimos la causa raíz.”
La causa principal: Desfase en los tiempos
El Asombroso Keni:
“La grieta estaba ocurriendo durante la expansión del agujero.
El material alcanzó su límite de estiramiento porque el exceso de material no fluía lo suficientemente rápido.”
AI Steel Cat:
“¿Entonces necesitamos acelerar el flujo del material?”
El Asombroso Keni:
“Exacto. Modifiqué la forma de la punta del punzón para incluir una superficie plana.”
AI Steel Cat:
“¡Bien pensado! ¿Funcionó?”
El Asombroso Keni:
“Sí, la grieta se redujo significativamente. También añadimos una protuberancia guía en el centro del punzón para evitar desalineaciones.”
AI Steel Cat:
“¡Eso es genial, Keni! ¡La sabiduría de los expertos brilla aquí!”
Conclusión
Esta vez, la causa fue un desfase en los tiempos de expansión del agujero e ‘ironing’.
Gracias al trabajo en equipo entre Keni y AI Steel Cat, el problema fue resuelto, y la producción volvió a la normalidad.
1. Información general: Causas de las grietas en el proceso de barreling
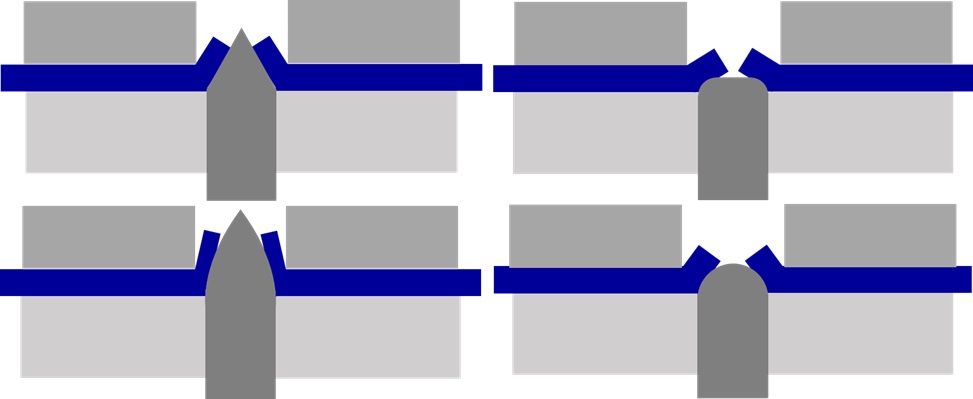
Entre las causas comunes de las grietas en el barreling se encuentran las siguientes:
- Límite de estiramiento del material:
Cuando la brida se estira demasiado durante el procesamiento, pueden aparecer grietas. - Rebarba en el agujero:
Si la rebarba está en el exterior, es más probable que se produzcan grietas en la pieza. - Estiramiento localizado:
Los materiales duros tienden a agrietarse cuando se produce un estiramiento excesivo en puntos específicos. - Condiciones inadecuadas de procesamiento:
Una velocidad de procesamiento o una selección incorrecta del aceite de corte pueden causar grietas.
2. Factores específicos señalados por Keni
Factores de procesamiento:
- Desalineación del agujero: Incluso un desvío de 0,1 mm puede aumentar el riesgo de grietas.
- Rasguños en el punzón: Los rasguños en un lado del punzón pueden desviar el centro del barreling, provocando grietas.
- Dirección de entrada: Si el punzón entra desde el lado con la cara dañada, la rebarba tiende a salir hacia el exterior, causando grietas.
- Fractura en el borde del agujero: Esta condición puede ser un detonante para la aparición de grietas.
Factores relacionados con el punzón:
- Forma de la punta del punzón:
Existen diferentes tipos, como la forma de bala, cónica, semi-redonda o plana, y cada una genera distintos patrones de grietas. - Rugosidad de la punta:
Si la punta del punzón está rugosa, el procesamiento se verá afectado negativamente.
Otros factores:
- Velocidad de procesamiento: La velocidad inadecuada aumenta la probabilidad de grietas.
- Lubricación: La lubricación únicamente con rodillos puede ser insuficiente, causando falta de aceite en zonas críticas. El tipo y la cantidad de lubricante también influyen.
3. Detalles del caso actual
Condiciones de procesamiento:
- Material: SPCE, espesor 0,8 mm
- Diámetro del agujero: Φ2,4 (para roscado M5, agujero inicial Φ4,57)
- Forma del punzón: Tipo bala
- Estructura:
- Inferior: Punzón de barreling con un stripper localizado.
- Superior: Coma receptora del barreling y mecanismo de separación.
Otros procesos:
- El mismo proceso incluye pequeñas curvaturas, curvaturas angulares y 18 puntos adicionales de barreling que pueden afectar el resultado.
Lubricación: Lubricación con rodillos (sin lubricación localizada).
Equipo: Prensa progresiva de 400 toneladas, SPM 25.
4. Contramedidas implementadas y resultados
A pesar de las siguientes medidas, el problema no se resolvió:
- Pulido de la punta del punzón.
- Reparación de las rebarbas y superficies de fractura en el agujero.
- Adición de lubricación localizada.
- Investigación del tiempo y movimiento del material (sin anomalías).
- Inspección del estado del stripper superior (sin problemas).
- Verificación de la alineación entre el punzón y el dado (todo en orden).
- Ajuste de la posición del punzón en 0,5 mm—sin mejora.
5. Observaciones del fenómeno de la grieta
A partir de nuevas observaciones, se identificaron los siguientes puntos:
- Las grietas eran más pronunciadas en el lado con menor proceso de ‘ironing’.
- Las grietas se desarrollaban desde dos puntos y no en la parte con mayor compresión.
- Se confirmó que las grietas avanzaban antes de la etapa de ‘ironing’.
6. Identificación de la causa
Los resultados de la investigación determinaron que el problema estaba relacionado con el desfase en el tiempo de expansión del agujero.
La solución se centró en acelerar el flujo de material en la punta del punzón durante esta expansión.
- Contramedida efectiva:
Rediseñar la punta del punzón para sincronizar mejor los tiempos de expansión e ‘ironing’.
Además, se observó que la inclinación del stripper causaba contacto lateral, lo que agravaba las grietas.
Dado que no era posible una modificación estructural, se decidió optimizar la forma de la punta del punzón.
7. Contramedida adoptada
Se cambió la forma de la punta del punzón a un diseño con superficie plana, que acelera el proceso de ‘ironing’.
Aspectos a considerar:
- Este diseño puede causar desalineaciones entre el punzón y el dado.
- Para prevenir esto, se añadió una protuberancia guía en el centro del punzón.
8. Conclusión
La causa raíz del defecto fue un desfase en los tiempos de expansión del agujero e ‘ironing’.
La modificación en la forma del punzón redujo significativamente la formación de grietas, incluso cuando la inclinación del stripper no pudo ser completamente corregida.
Sección extra: Efecto de la forma del punzón en el proceso
Según la información técnica de Misumi, las puntas de los punzones para barreling suelen tener una forma de bala. Sin embargo, se ha demostrado que otras formas también influyen en los resultados.
Puntos clave:
- La forma del punzón afecta la altura del barreling y la fuerza de procesamiento, desempeñando un papel crucial en la prevención de grietas.
- La sincronización entre la expansión del agujero y el inicio del ironing es fundamental.
- Formas que aceleran el ironing mejoran el flujo de material y reducen el riesgo de grietas.
Ajustar cuidadosamente la forma del punzón puede mejorar la estabilidad del proceso y minimizar los defectos. ¡Estos ajustes técnicos pueden marcar una gran diferencia en el éxito del barreling!