導入ナレーション
またしても発生したバーリング加工の「割れ」。
「こんなんじゃ生産が進まん!」と現場で怒号が飛び交う。
そんな中、立ち上がったのは、非凡ケニとAI猫生!
今回は前回とは一味違う割れに挑むことに――。 解説あり
対話パート:割れの原因を徹底追及!
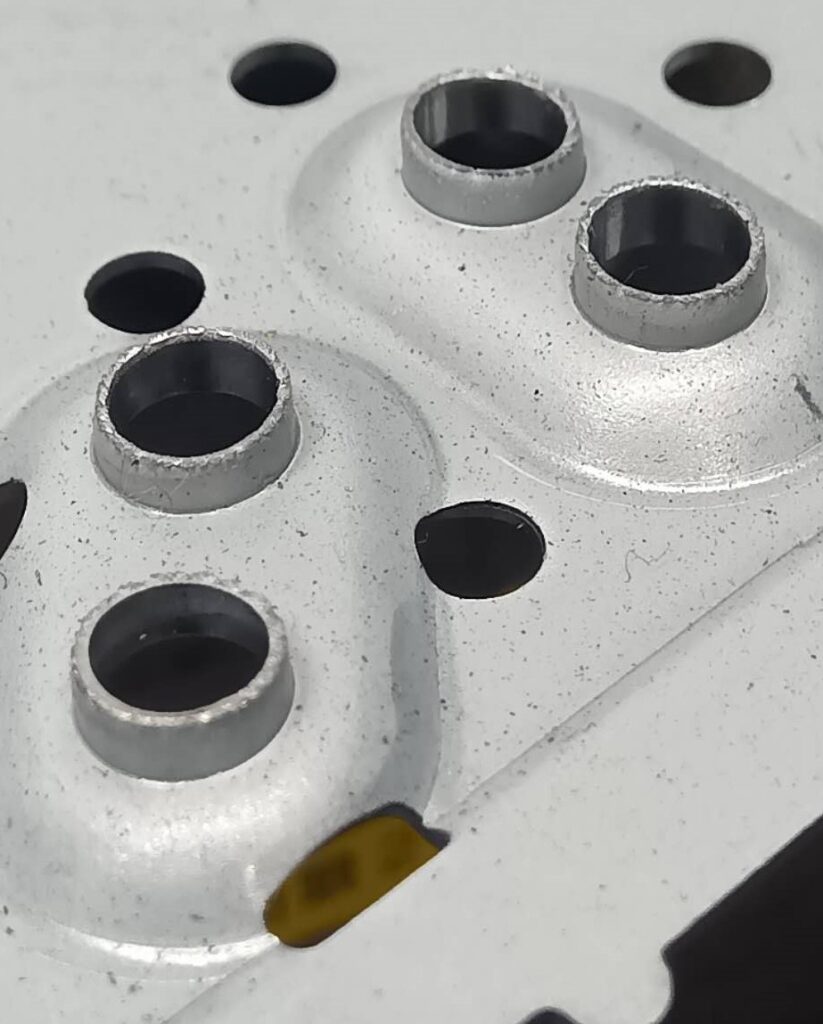
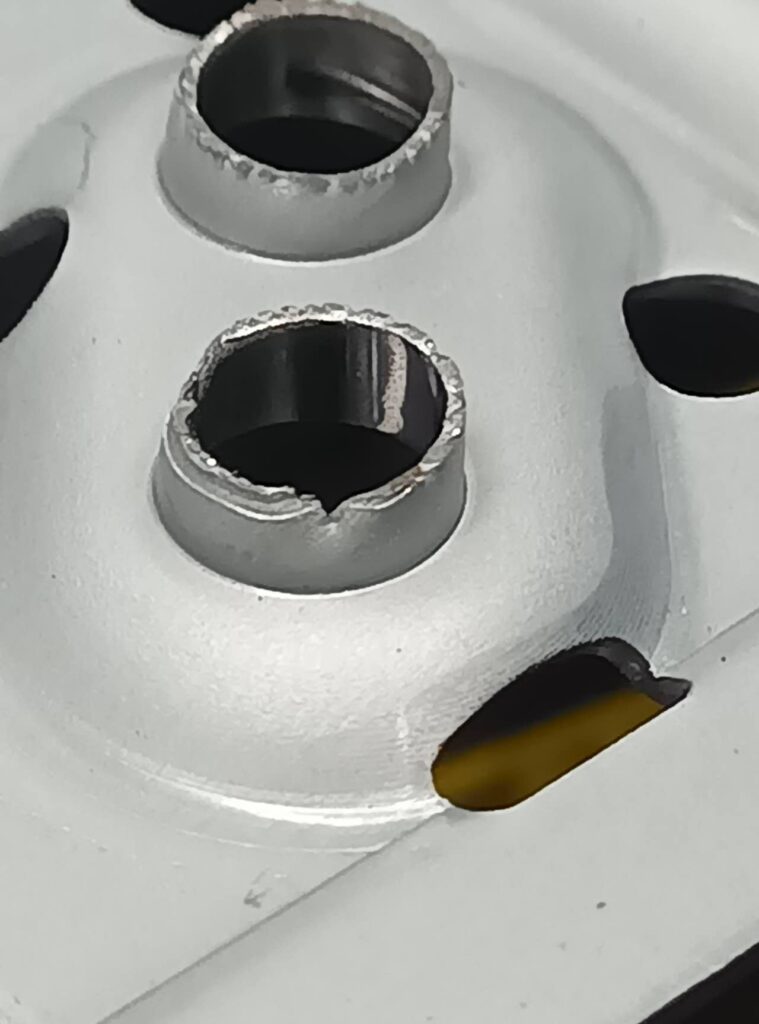
非凡ケニ:
「おい、AI猫生!割れがまた出たぞ!しかも、今回はなんか様子が違うんだ。どうなってんだよ!このバーリング割れ!読者のみんなならどうする?頼むから教えてくれよ~」
AI猫生:
「おっと、これは緊急事態ですね。まずはネット情報を振り返りましょう!」
- 材料の伸び限界:加工中にフランジが伸びすぎると割れます。
- 下穴のバリ:バリが外側にあると、割れが発生しやすいです。
- 局部的な伸び:硬い材料では局部的な伸びが限界を超えて割れます。
- 加工条件が不適切:加工速度や加工油が悪いと割れます。
非凡ケニ:
「確かにその通りだが、それだけじゃねぇんだよなぁ。」
視点を変えろ!前回の割れとの違い
AI猫生:
「そういえば、前回もバーリング割れが出ましたよね。
その時は下パンチのガタツキが原因で、ストリッパーコマやスプリングを強化しましたよね?」
非凡ケニ:
「ああ、よく覚えてるな。確かに前回も似たような現象だった。」
AI猫生:
「じゃあ今回も同じ原因じゃないんですか?」
非凡ケニ:
「いや、今回は明らかに違う。割れの位置と割れ方が前回とは違うんだよ。」
AI猫生:
「割れの位置と割れ方が違う…?」
非凡ケニ:
「そうだ。前回はパンチがガタついたせいで、均等に広がるような割れだった。
でも、今回は割れが2か所から進展してて、しかもシゴキ前に進んでる。」
AI猫生:
「なるほど…それじゃあ、シゴキ自体の問題ではない、と。」
非凡ケニ:
「その通りだ!だから、別の要因を考える必要がある。」
現場ならではの複合要因を掘り下げろ!
AI猫生:
「非凡ケニさん、現場独自の要因を整理しましょう!例えば――」
- 下穴の位置ズレ:ほんの0.1mmズレても割れやすくなる。
- パンチの傷:片側に傷があれば、中心がズレてしまう。
- ダレ面側からのパンチ進入:バリが外側に出て割れの原因になる。
- パンチの形状:砲弾型、テーパー型、半円型…形状によって割れ方が異なる。
- 面粗さ:先端加工部が荒れていると致命的だ。
非凡ケニ:
「おう、まさにそれだ。それに加えて、局部給油の不足や、加工速度が影響する場合もある。」
これまでの対策も総チェック!
AI猫生:
「では、これまでにやった対策を振り返ってみましょう!」
非凡ケニ:
「よし、これがこれまでの対策だ――」
- パンチ先端部の磨き直し
- 下穴のバリ修正
- 局所給油の追加
- 材料押さえのタイミング調査(異常なし)
- ストリッパー受けコマの状態確認(異常なし)
- パンチ・ダイの同軸度確認(問題なし)
- パンチ位置の0.5mm調整:効果なし
AI猫生:
「これだけやってもダメですか…これは手ごわい!」
非凡ケニ:
「だろ?だから、徹底観察した結果、ついに原因が見えてきたんだよ。」
原因の核心:タイミングのズレ
非凡ケニ:
「割れが発生してたのは『下穴を広げるタイミング』だった。
局部的な伸びが限界を超えて、余肉が足りなくなってたんだ。」
AI猫生:
「ほほぅ、ということは、余肉を早く送る必要がありますね?」
非凡ケニ:
「その通りだ。そこでパンチ形状を平面付きに変更してみたんだ。」
AI猫生:
「なるほど、それで割れは改善したんですか?」
非凡ケニ:
「おう、割れがかなり減った。さらにパンチ中央部にガイド突起を設けて、
位置ズレも防止したから、現場は安定してきたぜ。」
AI猫生:
「さすが非凡ケニさん、現場の知恵が光りますね!」
まとめナレーション
今回の割れ原因は、加工タイミングのズレとストリッパー傾きによる影響だった。
非凡ケニとAI猫生のチームワークで、不具合は見事解決!
現場は再び順調な生産を取り戻したのであった。
非凡ケニ:
「これで安心して生産が続けられるな!」
AI猫生:
「割れ、もう割れませんね!現場の冒険はまだまだ続きますよ!」
非凡ケニ:
「そうだな…。割れは我らの永遠のテーマだな!」
結びの一言
今日も現場に平和をもたらした非凡ケニとAI猫生。
読者の皆さん、明日も笑顔と技術で現場を支えていきましょう!
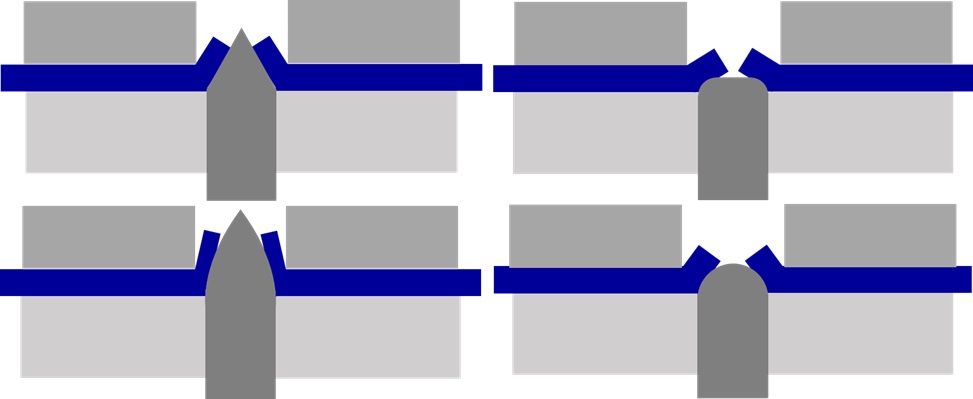
1. ネット情報:バーリング割れの原因(一般的に言われていること)
バーリングが割れる原因として、次のようなことが挙げられます:
- 材料の伸び限界を超える:
バーリング加工時、フランジ部分が伸びすぎると割れが発生します。 - 下穴のバリが影響する:
下穴のバリが外側にあると、伸ばされる部分が割れやすくなります。 - 局部的な伸び:
硬い材料をバーリングする際に、先端部分が割れることがあります。 - 加工条件が不適切:
加工速度や加工油の選定が不適切な場合、割れが生じることがあります。
2. ケニさんが挙げた具体的な原因要因
- 加工要因
- 下穴の位置ズレがあると、割れやすくなる。
- パンチの片側に傷がある場合、そちら側に引っ張られてバーリング中心がズレる。
- バーリング方向:下穴のダレ面側からパンチが入ると、バリ面が外側になりやすい。
- 下穴の破断面が割れの引き金となる。
- バーリングパンチの要因
- パンチ先端形状:
代表的には砲弾型、テーパー型、半円型、平面型がある。それぞれの形状で割れ方に違いが出る。 - パンチ先端部の面粗さ:
パンチの先端加工部が荒れている場合、加工に影響する。
- パンチ先端形状:
- その他の要因
- 加工速度が合っていない場合、割れが起きやすい。
- 給油方法:ローラー給油のみでは局所的な油不足が生じる。油の種類や量も影響する。
3. 今回の事例の詳細
- 加工条件
- 被加工材:SPCE t0.8
- 下穴径:Φ2.4、M5転造タップ用(下穴φ4.57)
- パンチ形状:砲弾型
- 構造:
下にバーリングパンチ、局所ストリッパー設置。
上ストリッパーにバーリング受けコマとノックアウト(剥がし機構)を設置。 - 他加工工程:
小曲げ、角度曲げ、他のバーリング(計18か所)が影響を及ぼす可能性あり。 - 給油方法:ローラー給油のみ(局部給油なし)
- 使用機材:400T順送プレス機、SPM 25
4. 改善対策の実施内容と結果
以下の対策を実施しましたが、問題は解決せず:
- パンチ先端部を磨き直し。
- 下穴の状態改善(破断面やバリの修正)。
- 局所給油を追加。
- 材料押さえのタイミングと動きの調査(異常はなし)。
- 上バーリング受けコマの状態確認(問題なし)。
- パンチとダイの同軸度を調査(問題なし)。
- パンチを意図的に0.5mmずらして加工:
割れの反対側にずらしても効果なし。
5. 不具合現象の観察から気づいた点
- 割れは、シゴキ(仕上げ加工)の少ない側から大きく発生。
- 割れが2か所から進展しており、最も扱かれている反対側からではなく、そこから離れた位置に割れが生じている。
- シゴキ前の段階で既に割れが進行していることが判明。
6. 原因の特定
これまでの調査結果から、次のことが判明しました:
- 割れの原因は「下穴を広げるタイミング」にある。
- 対策:
下穴を広げる際、先端部に素早く余肉を送ることで割れを抑制可能。
→ 先端部形状の見直しが最も効果的と判断。 - ストリッパーの傾きによって、パンチが片当たりを起こし割れが拡大している。
- 構造的な改造は困難なため、パンチ先端形状を変更する対策を採用。
7. 採用した対策
- パンチ形状を、シゴキを早める「平面付き形状」に変更。
- 注意点:
- 下穴とのズレや、ダイ・パンチ間の同軸度に狂いが生じる可能性がある。
- 対策として、パンチ中央部にガイド突起を設け、位置ズレを防止する工夫が必要。
8. 結論
- 今回の不具合原因は、バーリング加工における「シゴキタイミング」と「下穴拡大タイミング」のズレ。
- 改善策として、バーリングパンチの先端形状を工夫し、余肉を素早く送ることで割れを防止。
- ストリッパーの傾きが完全に直せない状況下でも、この形状変更により割れを大幅に軽減することができた。
●最後におまけ。
バーリングパンチ形状の影響と効果
ミスミ技術情報によると、バーリングパンチの先端形状にはいくつかの種類があり、一般的には砲弾型がよく使われます。しかし、他にも形状によって加工結果が変わることが分かっています。
形状の違いは、バーリングの高さや加工力に影響を与え、特に割れ対策として重要な役割を果たします。
ポイントは「下穴を広げるタイミング」と「シゴキが始まるタイミング」。
- シゴキが早い形状は、余肉が素早く送られるため、割れが発生しにくくなります。
- 形状を工夫することで、加工の安定性が高まり、割れのリスクを軽減できます。
バーリング加工では、このような細かな形状調整が成果を大きく左右するのです!